Cooling system upgrade cuts energy costs and boosts efficiency at polymer plant
Published: 19 November, 2024
Polypipe Building Services has significantly cut energy costs by up to £36,000 annually with the installation of a new process water cooling system at its Aylesford plant. Designed by Isocool and incorporating Eurochiller’s free air coolers, the system reduces energy consumption by utilising ambient air for cooling.
Polypipe Building Services is saving up to £36,000 per year in electricity costs thanks to a new process water cooling system at its polymer pelletising plant in Aylesford. The new cooling system was designed and installed by Isocool and incorporates free air coolers
manufactured by Eurochiller, both of which are part of the Atlas Copco Group.
Polypipe Building Services specialises in the design and manufacture of above-ground drainage and supply systems, including the well-known industry brand Terrain. The chiller plant at its site in Aylesford is a vital part of the business, supplying the polymer mixing and pelletising process with cold water. Failure of the system could result in significant costs to keep production going whilst repairs or a replacement was arranged. The existing chillers were more than 20 years old and needed to be replaced. This offered the opportunity to upgrade to a more efficient system, but it also raised a number of challenges.
Jim Pullar, Polypipe Building Services Site Services Manager, explained: “The replacement cooling system needed to be completed in the shortest timeframe possible to minimise downtime and avoid expensive disruptions to our manufacturing process. We only had a two-week shutdown window during which the replacement chiller and associated pipework all had to be completed. In addition, the chiller plant sits within a room which presents a very confined space to work in. This also means that the connecting pipework needs to change direction several times.”
Pullar called in Isocool, who installed and maintained the original system and continues under the name of Atlas Copco to be Polypipe Building Services’ cooling supplier of choice, to support the upgrade.
Cooling requirements
Temperature control is critical to the quality of Polypipe Building Services products. Polymer production at the Aylesford site uses two-stage mixers (hot and cold). The polymer is blended at an optimum temperature of over 100°C before passing into a cold mixer for rapid cooling to 50°C. Once cooled, the polymer is then pumped to dry blend silos, pelleted and extruded into shape.
Each batch takes approximately eight minutes to process. Polymer production of this scale requires cooling water at a constant temperature of 15°C and a flow rate of 80m3 / hour. This equates to 200kW per chiller.
To improve efficiency and reduce energy consumption, Polypipe Building Services decided to upgrade the chiller plant to a new ‘free air’ system. This means that when the ambient air temperature falls below a set temperature, the chillers switch off and use the outside cool air to chill the water.
Cooling system configuration
Isocool designed, specified and installed a new cooling system to meet the specification and address the confines of the existing plant room.
James Cowen, Regional Sales Engineer, Process Cooling Solutions at Atlas Copco, said: “Our primary focus is always on delivering the best value for our customers. For this project, we used a combination of Eurochiller products and third-party equipment to address the space restrictions and deliver the cooling levels that the application demanded.”
The main cooling plant comprises a Eurochiller DC 400/L AD self-draining free air cooler and a Eurochiller ADC 500/L adiabatic cooler. Sited on the roof, both these chillers are designed to withstand harsh external environments. The free air chiller is programmed to switch to ambient air cooling if the temperature falls below 15°C. The adiabatic cooler uses a special pad rather than spray bars, which eliminates water droplets from the air stream. Combined with one-time water use, this dramatically reduces the risk of legionnaire’s disease and lowers maintenance requirements. Two water-cooled chillers further reduce the process water temperature prior to it being introduced into the cold mixers.
In addition to the main chiller equipment, Isocool supplied ancillaries including a new water storage tank and replaced all the recirculation pumps and associated pipework. Unusually, they did not use traditional metal pipes for the task because the physical constraints of the plant room made welding steel pipework problematic. However, Polypipe Building Services supplies a plastic piping system called MecFlow, which offered a potential solution.
Cowen commented: “It’s not every day you are able to showcase a customer’s product as part of a system upgrade, but we seized the opportunity. We had to allow for the insertion depth of the MecFlow weld joint, which was a slight change to working with stainless steel, but following training with Polypipe Building Services, our team was able to achieve a seamless join and the system works very well.”
Despite all the time, space and technology challenges they encountered, Isocool succeeded in removing the old plant and installing and commissioning the new plant within the two-week shutdown period. This included the construction of a temporary platform around the roof to support the new cooler during installation.
Pullar concluded: “Atlas Copco Isocool delivered for us on every level. We hit our maintenance window, we have a fully upgraded process water cooling system, and we have reduced our energy consumption significantly, which is a great return on investment.”
For further information please visit
www.atlascopco.com/en-uk/compressor
https://twitter.com/atlascopcogroup
https://www.linkedin.com/company/atlas-copco-group/
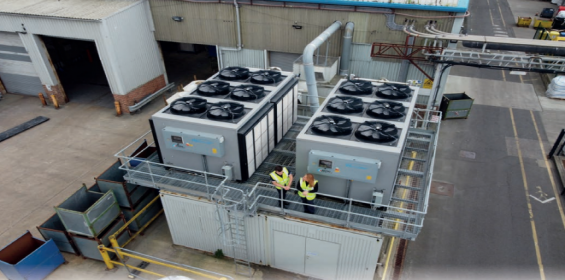