Addressing the skills gap in the face of climate change
Published: 11 November, 2024
A recent Institution of Engineering and Technology (IET) survey reveals a significant skills gap in the engineering sector, particularly in the context of addressing climate change. While many UK employers are taking steps to reduce their environmental impact, there is widespread concern about the lack of necessary skills and training within the workforce. Etienne Fourie, Technical Sales Manager at Babcock Wanson, takes a closer look.
A new international survey1, published at the end of 2023, by the Institution of Engineering and Technology (IET) confirms what the engineering sector has been saying for years: that a considerable skills gap exists which impacts productivity. What’s particularly interesting to note from this latest survey is that, in the face of climate change, that gap feels more like a chasm.
According to the survey, two thirds of UK employers are concerned about climate change and most have made a technological or organisational change to lower their environmental impact in the last three years, primarily focussed on emissions reductions. However, around three-quarters think their organisation does not have the full skillset to be resilient against climate change, and 29% feel their organisation is not agile enough to adapt. Furthermore, they cite increased costs in their supply chain because of climate change which, ironically, is seen as a widespread barrier to becoming net zero.
The findings of this survey is supported by the government’s November 2023 research briefing, ‘The UK's Plans and Progress to Reach Net Zero by 2050’. It states that the industrial sector was responsible for 14% of UK emissions in 2022, with the Climate Change Committee 2023 Progress Report considering there to be higher risks to decarbonisation than in 2022, with insufficient plans for the majority of the Carbon Delivery Budget Plan targets for the fifth and sixth carbon budgets due to a continuing lack of progress.
UK Engineering employers surveyed by the IET largely put the blame for the skills gap on the education system. 63% think the UK education system does not prepare young people to work in their industry. However, the engineering sector also has a role to play here by providing appropriate training and quality apprenticeship schemes.
To make these changes will take political willpower, time and investment. But time is one thing we are running short of when it comes to climate change and the UK’s 2050 Net Zero goal. We need to act now to decarbonise industry.
With process heating being a major consumption of energy and source of emissions within industry, it’s an area that manufacturers and engineering firms across the UK – and the world – are focussing their decarbonisation efforts and resources on. Inefficient boilers and burners are being replaced with modern energy efficient heat raising equipment and systems that incorporate heat recovery, and we are seeing a big move towards electric powered systems, away from fossil fuel.
But as we make these changes, the skills to operate and manage much of this equipment is in short supply as we have clearly seen. So, if the skills aren’t readily available, what options does industry have? The answer has to be to reduce or remove the skills required, which is where manufacturers such as Babcock Wanson have a role to play. We can’t solve the skills gap but we can engineer some of the skill out of day to day operation. Here we suggest four ways to help bridge the skills gap:
1 Thermal fluid heaters Increasingly popular, thermal fluid heaters work at high temperatures in a simple closed loop. When compared to a steam system this means no change of state of the fluid so no condensate and therefore no flash steam losses, no blow down losses or make up water required, no effluent discharge and completely corrosion free without the need for expensive chemical treatment. Not only are they more energy and cost-effective but in the context of the skills gap they are much easier to operate daily. Furthermore, they operate outside the Pressure Systems Safety Regulations as the fluid is not maintained in the liquid phase by pressure, so are safer.
Across Europe and now in the UK there is a move towards electric thermal fluid heaters, such as own newly launched EPC EL which, being modular, can be configured in series and parallel to meet different applications and site requirements.
2. Unattended boiler operation
Where thermal fluid heaters are not an option, steam generators remain, but these require a far higher level of skill to operate. Some of this can be mitigated by introducing unattended boiler operating systems. Traditionally these were used by organisations whose operational hours extend beyond the standard. However, recent years have seen a considerable acceleration in both the popularity of these systems (our customers now ask for it as standard) and the length of time they are able to safely operate unattended, from three to seven days. Systems, such as our own BW7DAYS, make for easier operation requiring less skill. Once set up for unattended operation, all the user needs to do is monitor for any operational alarms and undertake a very simple 15-minute test every three or seven days, which is completed without interfering with boiler operation and is acknowledged to the boiler control system, thereby ensuring the tests are completed to the operating schedule. Improved safety and conformance with current and future UK & EU legislation is also a key benefit and one that even 24/7 operational sites that are fully staffed are increasingly attracted to.
3. Water treatment services
All steam raising equipment requires the feed water to be treated to prevent corrosion. Both the quality of the steam and the longevity of the boiler producing it are completely dependent upon the condition of that water feed. Poorly prepared water can cause rapid and costly damage to the heating surface and can lead to the end of a boiler’s working life in a short period of time. Water treatment is a skilled task, so consider outsourcing this.
4. Outsource maintenance Regular service and maintenance are essential for steam plant to ensure smooth operation and safety, but even thermal fluid heating systems benefit from regular servicing. Being able to operate such a system does not mean you have the skills to maintain it. Outsourcing this to a specialist, or the manufacturer itself, ensures the work is conducted to a professional level by experienced, trained service engineers.
1 theiet.org/greenskills
Babcock Wanson has partnered with water treatment specialists Deep Water Blue to provide water treatment services for steam-raising equipment. Additionally, its vSteam web portal allows customers to enter daily readings online and receive real-time feedback support between scheduled consultancy visits.
For more information, please visit: www.babcock-wanson.com
https://twitter.com/babcockwanson
https://www.linkedin.com/company/babcock-wanson/
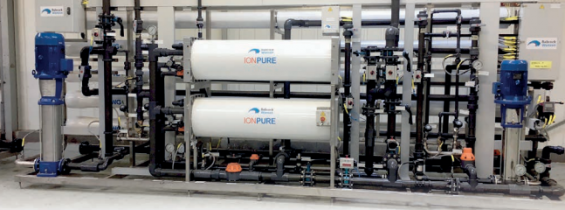