New Report Focuses on Optimising Maintenance Strategies through Improved MRO Supply Chain Management
Published: 13 August, 2024
While effective maintenance strategies and regimes rightly take centre stage for plant engineers and reliability teams, a new industry report emphasises that optimising the supporting MRO (maintenance, repair, and operations) supply chain should also be a crucial priority.
The MRO Supply Chain Report 2024 highlights the significant impact of MRO supply chain challenges on maintenance regimes and overall operational efficiency. Smart Machines & Factories looks at the key findings from the report, focusing on the implications for maintenance professionals and offering strategies to optimise maintenance practices through improved MRO supply chain management.
The report paints a stark picture of the current state of skills in the maintenance industry. Experienced engineers are increasingly hard to find, and this scarcity is reflected in the small sizes of maintenance teams. According to the report, 67% of maintenance teams consist of fewer than 10 people, while 70% of engineering stores departments have under 4 staff members. This shortage of skilled personnel forces engineers to take on roles outside their core responsibilities, including involvement in MRO procurement and managing engineering stores.
The lack of specialised skills in these critical areas can lead to inefficiencies and increased downtime. With small teams stretched thin, there is little time for training or knowledge transfer to less experienced colleagues, exacerbating the skills gap. To mitigate these challenges, many businesses are turning to outsourcing. Outsourcing allows companies to leverage the expertise of vendors who can offer both technical and supply chain knowledge, enabling engineers to focus on their primary tasks and reducing the strain on limited in-house resources.
Moreover, the report highlights that 10% of businesses have resorted to involving engineers in stores duties due to the acute shortage of resources. This practice not only diverts engineers from their core tasks but also indicates a critical need for better resource allocation and management within the MRO supply chain.
Financial impact
The financial implications of poorly managed MRO inventory are significant. The report reveals that over half (51%) of UK manufacturers experienced unplanned downtime in the past year due to spare parts availability issues. This downtime translates directly into lost production time and financial loss. The trend of stockpiling MRO inventory as a buffer against supply chain disruptions has led to substantial financial burdens. The average UK manufacturer now holds £730,681 worth of MRO inventory, a figure that has increased dramatically since 2019.
Despite the large stockpiles, many businesses struggle with inventory management, leading to high levels of obsolescence. Over 50% of respondents could not provide data on the value of engineering inventory written off in the last financial year due to obsolescence. The frequency of regular stock checks and cycle counts has also declined, with 30% of businesses never performing full inventory audits. These practices result in excessive write-offs and inflate carrying costs, further draining profitability. There is also the possibility that many businesses are storing up something of a ‘write off timebomb’ which, when its full impact is exposed, will have serious implications for their financial reporting.
The report underscores the need for businesses to adopt more disciplined inventory management practices. The decline in regular stock checks and the prevalence of obsolescence highlight a significant area for improvement. Implementing more frequent cycle counts and leveraging technology for inventory management can help businesses maintain accurate stock levels, reduce write-offs, and optimise carrying costs.
Procurement challenges
One of the most striking findings from the report is the prevalence of “squirrel stores”—unofficial stashes of parts kept by engineers and technicians. A startling 55% of respondents admitted to having such stores, highlighting a significant trust issue with official procurement and stores processes. These squirrel stores undermine data integrity and complicate inventory management.
Additionally, the involvement of engineers in procurement activities, driven by the lack of dedicated resources in engineering stores, further complicates the procurement process. Engineers often do not have the necessary procurement expertise, leading to inefficiencies and potential errors. The report encourages a more structured approach to procurement, with clearer roles and responsibilities to ensure that engineers can focus on their core tasks while the MRO stores team and the procurement team work in sync to handle purchasing.
The report also highlights that the “squirrel stores” phenomenon is symptomatic of deeper issues within the procurement process. Engineers’ lack of trust in the procurement team and the perceived inefficiency of the stores system drive them to create these unofficial stores. By addressing these underlying issues and implementing more efficient inventory management systems, businesses can improve trust in the official processes and reduce the need for such workaround solutions.
Performance measurement
The performance of engineering stores is often measured using backward-looking metrics such as work order completion rates and stock availability. While these metrics are important, they do not capture the full potential of what a well-managed MRO supply chain can offer. The report highlights the need for more innovative and proactive performance measures that focus on technical expertise and supply chain insight.
For instance, the time taken to source and order a non-stocked spare part is a critical metric that directly impacts downtime. The report found that sourcing such parts often takes days, causing significant production delays. By integrating supply chain knowledge and technical expertise into the engineering store’s function, businesses can reduce these delays and improve overall efficiency.
The report suggests that engineering stores should not just be measured on traditional metrics but also on their ability to add value through technical and supply chain insights. For example, the MRO stores team can play a crucial role in suggesting alternative parts or suppliers, thus reducing lead times and costs. Businesses that harness the full potential of their MRO stores team can significantly enhance their operational efficiency and reduce downtime.
Business impact
Aligning maintenance strategies with MRO procurement and engineering stores operations can have a profound impact on reducing downtime and enhancing profitability. The report emphasises that issues related to the MRO supply chain and engineering stores are major causes of downtime. By addressing these issues holistically, businesses can gain valuable insights into the root causes of downtime and implement measures to prevent it.
There is no one-size-fits-all solution to these challenges, but a well-coordinated approach that aligns maintenance strategies with MRO procurement and engineering stores operations can lead to significant improvements. For example, adopting predictive maintenance strategies and leveraging data analytics can help businesses anticipate spare parts needs and reduce unplanned downtime.
The findings also highlight the importance of viewing the MRO supply chain as an integral part of the overall maintenance strategy. By integrating MRO practices with maintenance programmes, businesses can create a more resilient and efficient operational framework. This integration helps in ensuring that the right parts are available when needed, thus reducing downtime and improving overall productivity.
The MRO Supply Chain Report 2024 from ERIKS UK & Ireland provides crucial insights into the challenges faced by UK manufacturers in managing their MRO supply chain. For maintenance professionals, the report underscores the importance of addressing skills shortages, improving inventory management, and optimising procurement processes. By aligning maintenance strategies with MRO procurement and engineering stores operations, businesses can reduce downtime, enhance efficiency, and ultimately increase profitability.
https://www.linkedin.com/company/eriks-uk/
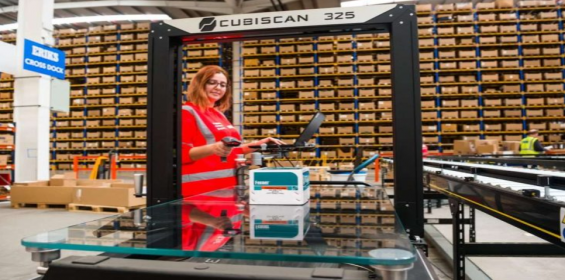