Want a safer workplace? Then show the value
Published: 21 August, 2023
Having recently achieved the ISO 45001 certification for Air Products, Rachel Rawlings*, talks about why plant operators and engineers are central to the success of occupational health and safety initiatives.
In a bustling industrial landscape where plants operate around the clock, a deep commitment to health and safety should be etched into the very fabric of any modern company.
My company recently achieved ISO 45001 for seven of our Air Separation Units (ASUs) – this is the international standard for management systems of occupational health and safety (OHS). The experience underscored the critical importance of plant managers, operators, and engineers in informing and supporting a robust and long-term approach to OHS. It became clear once again that in addition to tightening our procedures, working towards the standard also needed a strategic plan and a communications push right from the very top to bring all our teams on board and get them thinking not just about the what but the why.
Put simply, high standards of OHS are crucial for commercial success. A company’s clean bill of health on safety attracts and retains skilled staff as well as discerning clients, which protects the bottom-line as well as the reputation of the company.
Rather than it being extra work, we had to show the operators that keeping the plants running goes hand in hand with robust OHS – one complements the other. Instead of imposing more procedures and processes, we encouraged the plant managers to share their experience, obstacles and pain points with us so we could resolve them together. This consultation and dialogue and coming together to find workable solutions was key to successfully achieving the certification at all seven of our Air Separation Units (ASUs) in one go – no mean feat.
Commitment from senior leadership was another crucial component of ingraining the message of safety-first. Air Products’ management team put its weight behind the ISO 45001 process. They attended the opening and closing meetings with the ISO 45001 assessor in person, signalling the serious]ness with which the company views standards, procedures and ultimately, safety.
With buy-in from both on-site teams and the senior leadership team, it was then a matter of making sure the safety and quality procedures were easy to follow and accessible, so they are not a burden on anyone’s time. For example, we saved the generic procedures and risk assessments across all sites in one place – an easy to access shared site – to standardise these processes and ensure ease of access and use.
Another lesson learnt was that when it comes to safety, small changes can have big impacts. For instance, often in this industry, women end up having to wear men’s safety clothing, rolling up the trouser legs and arms to try and get it to fit. Working with our supplier to stock a capsule range of female fit and smaller fit fire-retardant workwear will ensure that the female workers are no longer an afterthought. It’s important if we are looking for a more diverse workforce, that we make them feel welcome, comfortable, and safe on site while upholding our safety standards at the same time.
But of course, having achieved what we set out to do with ISO 45001 is only half the battle won. The harder task is always to maintain the certification and not let things slide. And this is why a change of mind-sets in important at every level of the company because we can’t be lax – each of us has to make sure we are doing our bit so that we are always safe at work and audit ready.
To promote a culture of inclusivity and shared responsibility the work that goes into maintaining safety standards needs to be relatable and visible to everyone at the company. This helps everyone know why the work is important and what’s being done.
Internal social media channels are incredibly useful for this. Posting often and making sure the content is engaging, alive with images, personal anecdotes and humour will engagemore colleagues – who may not even be directly involved with OHS management.
Informal engagement such as this encourages everyone in a business to share their work, talk about what they find challenging, and where they see opportunities for improvement. From someone who orders equipment to the people who install it and make it operational, everyone’s opinion counts. Such casual conversations can often give precious insight into what needs tweaking and how best to go about it.
In conclusion, it’s quite simple: putting people’s safety first and ensuring high standards may seem a no-brainer but the journey to fostering a safety-conscious culture is neither swift nor effortless. It cannot be led by one team, in isolation. It cannot be imposed by the leadership. It is a collaboration where every team member plays a vital role and everyone’s voice must be heard, from the CEO and the seasoned plant veterans, right down to a rapidly diversifying workforce of newcomers.
*Rachel Rawlings is the Regulatory Affairs and Quality Manager for the UK and Ireland at Air Products
https://twitter.com/AirProductsuki
https://www.linkedin.com/company/air-products/
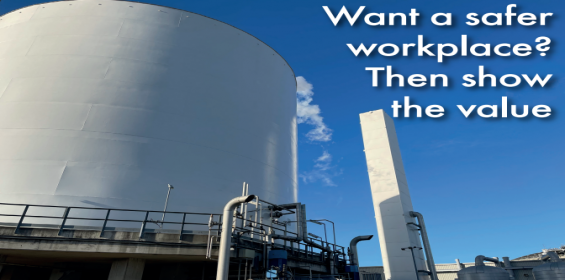