Implementing a proactive maintenance plan
Published: 30 April, 2021
David Stevens* outlines the benefits of adopting a digital condition monitoring programme, and the important role that ‘smart sensors’ play in improving reliability while delivering cost-efficiency.
The value of digital data collection from critical assets is increasingly being recognised by companies wishing to implement a proactive condition-based maintenance (CBM) plan. Digital condition monitoring (CM) can bring considerable benefits in terms of improved asset performance and lifespan, reduced downtime, increased safety on the plant floor and more productive use of personnel – all of which can have a significant impact on maintaining a strong bottom line.
There is a strong argument for making the shift from pen and paper to tablet or Android. However, collecting data digitally is one thing; extracting maximum value from that data is another challenge altogether. Therefore, any manager looking to take the crucial step towards digitalisation should consider very carefully the capabilities of the technological tools currently on the market, to ensure they get the best return on investment.
The selection of sensors - the device fixed to a rotating machine to take measurements such as vibration and temperature - is a very good place to start.
Limitations of fixed sensors
The old adage ‘you get what you pay for’ applies strongly to sensors. There are fixed sensors on the market with low price tags, but they offer only a basic level of monitoring, usually aligned to ISO standards for overall vibration levels. These sensors allow little, if any, user intervention or configurability. In many cases vibration levels are indicated on a simplistic red, amber, or green ‘traffic light’ system.
There are inherent limitations to this. An operative has to be physically walking past the machine to see any lighting alert. Once it is spotted, although the system might have issued an alert, there is no means of properly establishing what the issue might be, as there is no data to analyse.
Additionally, the sensor might be configured to take a reading every week, day or hour, so on a machine operating a batch process, and therefore running intermittently, it could potentially be taking readings when the machine is not operational.
By contrast, an advanced ‘smart sensor’ might demand a higher price, however, it also delivers a range of capabilities which bring condition monitoring well and truly into the 21st century.
Benefits of smart sensors Smart sensors, in conjunction with an advanced cloud-based CM system, can provide the bedrock for a proactive CBM programme and optimise the operational and financial efficiency of a plant by delivering:
Configurability
Detailed analysis
High data storage capability
Accessibility and hazard limitation
Configurability
An advanced smart sensor has inbuilt configurable features – Log Frequency, Running Detection and Wake Frequency – which enable it both to collect readings after a pre-determined time period, and to take readings only when the machine is running.
For example, after a specified time period, which can be anything from one hour to four weeks, the sensor ‘wakes up’, ready to collect a set of readings.
The Log Frequency, when readings are scheduled to be taken, might be set to one week. At that point, the sensor is programmed to respond to a predefined level of vibration which indicates the machine is running (Running Detection). If the sensor detects that the machine is not running, the Wake Frequency feature will continue to check, usually everyone or five minutes, until the sensor detects that the machine is running. At this point a full set of triaxial vibration readings will be taken.
This feature is particularly valuable for batch process applications, which run at intermittent intervals and potentially for very short periods of time.
Detailed data analysis
The cloud-based CM system, which stores the data collected from smart sensors, takes data analysis to an entirely different level.
For example, the most advanced sensor can be configured via the handheld device to a portal, which uses component templates with predefined vibration measurements.
This can facilitate different frequency ranges and lines of resolution for vibration measurements, depending on the rotational speeds of the components. While many sensors only work between 10Hz and 1kHz, a smart sensor can be configured to take readings up to 5.5kHz, delivering more information at a far greater range and enabling a more tailored CM solution where required.
It can also measure the components’ surface temperature, which is particularly useful for continuously running machines.
One of the major drawbacks of a pen and paper approach to asset management is the that readings might be taken but never used to inform a maintenance plan.
Digital data collection enables up to 5,000 readings to be stored securely in the cloud. An automated diagnostic assistant (ADA) provides real-time analysis and issues alerts which identify impending problems with a machine, and suggests pre-emptive action to avoid unscheduled downtime. This information can be accessed by any authorised personnel from their laptop, from any location in the world.
Improved accessibility, enhanced safety
There are assets and plant areas which have been no-go areas for many years due to their inaccessibility or hazardous nature – think gearboxes on agitator drive units, or assets in chemical environments. Fix a smart sensor onto these assets and inaccessibility becomes a problem of the past. Remote data collection via Bluetooth® from for example, an offloading pump or a solvent pump, removes the need for any operator to be in the vicinity.
Cost benefit analysis
The only real hinderance to switching to smart sensors is a reluctance to change age-old practices and the perceived capital cost implications of replacing pen and paper with digital tools.
However, there is a significant return on investment by investing in a digital CM programme. For example, one large chemical company saved £252,320 over 12 months by employing the Machine Sentry® online CM system, planning their maintenance instead of letting critical assets run to failure.
With smart sensors and digital data collection offering improved reliability, productivity and the potential for significant long-term cost benefits, companies wishing to stay ahead of the digitalisation curve should recognise that the time has come to consign pen and paper-based CM to the wastebin.
*David Stevens is technical authority and skills competence manager for AVT Reliability
For more information:
https://www.avtreliability.com/
https://www.linkedin.com/company/av-technology/
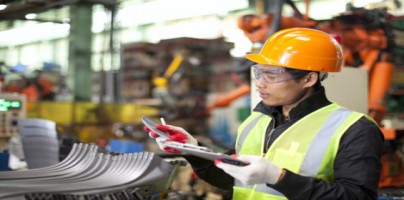