Exposing the software underbelly
Published: 06 August, 2020
Every moment that a production line or facility is shut down owing to technical problems is a major cost burden. Happily, most facilities today do have a coherent maintenance programme. However, many facility managers question whether preventive maintenance or predictive maintenance is best. In fact, best-in-class maintenance programmes incorporate both. PWE reports.
It may not make financial sense to install sensors everywhere and suitable technology may not always be available. In these scenarios, performing preventive maintenance on some assets at regular intervals (for example with a thermal imaging camera) may be the best approach.
But predictive maintenance is undoubtedly the future. Alerts are configured into analytical programs to notify users when assets are out of tolerance. When this happens, maintenance staff will utilise all the data to best implement plans to remove assets or schedule downtime. Facilities can be shut down assets at a planned time.
Predictive maintenance techniques powered by artificial intelligence (AI) are helping enterprises across industries to find patterns that can avoid machine failures. To reliably detect potential faults, a predictive maintenance system needs to have prior knowledge of all possible fault situations. By “teaching” the maintenance system about all the various possible fault situations, AI-based machine learning software enables it to detect specific faults in real-time and initiate remedial action.
"Unlike AI, traditional business intelligence systems are not designed to handle huge volumes of industrial Internet of things (IIoT) data," says Venkata Naveen, Disruptive Tech Analyst at data analytics company GlobalData. “Predictive maintenance is a key cost-saving digital strategy for any enterprise. AI-powered predictive maintenance can help enterprises to save money and time on maintenance, machine downtime while extending the life of their heavy equipment.”
If machines can talk and exchange data, then potential problems can be detected by running background AI-based software that can identify anomalies and other normally unforeseeable faults. Once the predictive maintenance system knows the exact point in the future at which a machine will be shut down for maintenance, it can automatically initiate the associated logistics processes. This ensures that all the relevant work and parts ordering processes are properly coordinated.
Mitsubishi Electric has developed AI-based diagnostic technology that harnesses machine learning algorithms to analyse sensor data from a machine and generate a model of its transition between different operational states. The model is then used to set optimal conditions for detecting abnormalities during each operational state, enabling operators to gauge signs of machinery failure before actual breakdowns. Also, by harnessing data from a sensor and using the drive to process the information into actionable insight, a Mitsubishi Electric 800 Series VSD will look after itself as well as the general health of a complete drive train.
“One of the critical challenges for predictive maintenance is streamlining the flow of data from machines to a central system with a low level of latency and high security, which, given the advancements in 5G connectivity and cybersecurity, can be overcome," Naveen concludes. "Despite the stumbling blocks, predictive maintenance is a vital part of an enterprise’s digital transformation strategy.”
Critical drives
By installing SmartCheck condition monitoring devices on 58 critical drives, Schaeffler’s European Distribution Centre, one of Europe’s most modern logistics centres, has benefited from reduced unplanned downtime, reduced maintenance costs and increased machine availability.
Inside the EDC Central are seven automated storage and retrieval systems, which continuously handle loads in various directions from storage racks with a height of around 38.5m. Any unplanned downtime due to bearing damage can affect the entire supply chain, but the bearings in the drives are subjected to severe loads during operation.
Of the 3,000 drives at Kitzingen, 58 of the most critical are now monitored using SmartCheck. Of these, 51 are installed on spiral conveyors and lifting stations, where they monitor bearing vibration, temperature and speed. Seven others are installed on the drives of the storage and retrieval systems. The devices are connected in turn to the network, allowing local visualisation in the control room.
After an operating period of around 18 months, one of the SmartChecks detected an irregular upward trend. The subsequent visual inspection carried out by local maintenance staff confirmed that grease had escaped from the track roller bearing. Due to the early detection of this irregularity, the site was able to schedule and perform the bearing replacement in good time and therefore prevent any unplanned downtime.
Ageing legacy assets
According to data collated by Sumitomo (SHI) Demag, there are approximately 15,000 injection moulding machines in the field in the UK. However, these are only being replaced at a rate of 650-700 new machines per year. This means that many injection moulders are still utilising ageing machines that arguably should have been traded in several years ago. This makes smart maintenance essential. covering both servicing and retiring equipment at the right time. A problem with driving an injection moulding machine ‘into the ground’ is that at some point the money spent on repairs can be of the same order as the cost of a new machine. Another risk is operating a machine that relies on obsolete parts - under EU law (at least), suppliers are required to ‘guarantee’ 10-year spare part availability.
"It might sound obvious, but the single biggest thing users can do to ensure machine reliability and longevity is to carry out the service work highlighted in the instruction manual!”, says Managing Director Nigel Flowers. "This mainly centres on basic maintenance tasks, such as lubrication and changing fan filters. Such tasks are simple to perform but often overlooked, with dire consequences. Planned maintenance invariably has less impact on line efficiency than unscheduled downtime caused by a failing part."
The next step is to move to a more predictive approach. The optimum time to change a part is just before it fails: now, this is entirely possible. The latest injection moulding systems can alert users in advance to what maintenance needs to be carried out and what parts need to be replaced.
According to Flowers, emerging technologies to further enhance machine reliability are on the horizon. RFID tags could potentially serve to assess health and performance. And Augmented Reality (AR) could be used in several ways to assist with machine support and diagnostics - for example, enabling in-house engineers to see what components are inside a cabinet without physically opening it. There is also scope for sharing machine data between suppliers and customers, providing security obstacles can be overcome.
Connecting remote assets
Companies are increasingly looking to connect remotely located assets for monitoring and control over the internet. However, often there is no local infrastructure to connect such assets to the internet.
HMS Networks’ Anybus Wireless Bolt IoT targets this very situation, providing reliable cellular-based internet connectivity over NB-IoT and CAT-M1 for remote assets that are otherwise hard to reach and connect.
Wireless Bolt IoT includes all elements needed to get stationary or mobile assets online over a cellular connection. It features a robust IP66/IP67 housing with UL NEMA 4X certificate for outdoor mounting, an integrated cellular antenna with a modem, a microcontroller and firewall.
Virtual sensors
What physical sensors cannot measure can often be done by using soft sensors – for example, combining multiple correlated parameters within formulae and using 'nested calculations'. The latest version of Software AG's TrendMiner extends these capabilities. The most important enhancements are improvements to OSIsoft PI integration, better analysis of operational performance and easy navigation through context items.
“All companies have been hit by global disruption to buying patterns and supply chains. However, they can still make their process manufacturing more efficient and productive," says General Manager Joan van de Wetering.
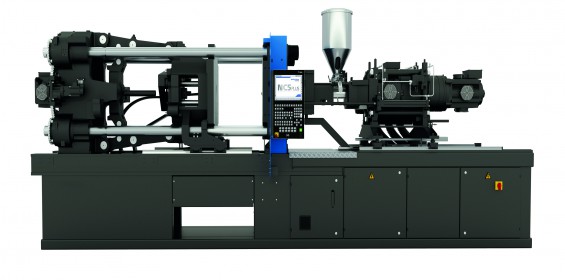