Managing food waste
Published: 19 December, 2019
Tobius Antius, CEO of food process automation company Novotek AB, explains how, with automation and systems, manufacturers can help to minimise the creation of food waste in manufacturing.
According to a report by Boston Consulting Group (BCG), food waste will be a $1.5 tn problem by the year 2050. But it’s not all bad news. The same report says that better supply chain infrastructure and efficiency could reduce this figure by $270 bn within the same timeframe.
How can food waste be reduced at the manufacturing stage of the supply chain? In an ideal world, there would be no food waste and manufacturers would be able to derive a perfect yield of production, relative to the ingredients put in. Nevertheless, food waste is an issue; albeit one that automation and optimisation technologies can help solve, including by maximising the efficiency of generating gas from food waste.
The food and beverage industries were late to adopt automation and plant IT. Yet progress has been made, and 50% of Europe’s recycling plants now feature automated processes.
Meanwhile, a recent report by PwC claims that, in the waste management sector alone, 62.6% of jobs have a chance of being automated by the year 2030 — the highest percentage in any sector. An upside is that quality and effectiveness of automation in the food industry is far higher than in other prominent industries.
But the downside is that many food plant managers are still experiencing a learning curve with new technology. One way to address this is with dedicated technical support of automation systems.
Technical support programs are often overlooked, or disregarded to some extent, by food manufacturers who consider it to be an additional service. In reality, it’s arguably the most effective way of ensuring your manufacturing IT investment offers long-term value.
However, for other food plant managers, the learning curve of onboarding automation systems can be attributed to a lack of defined purpose. In other words, managing waste through automation is about more than just installing new equipment. Food and beverage companies instead need to take an intelligent approach to deriving energising gas from food waste.
Customised modular approach
Novotek has found that solutions like Predix OPM allow firms to conduct analysis of the complex mix of factors that affect gas production. Through this analysis, they can learn the best ways to run digestion processes with different blends of food waste.
With SCADA systems, operations can make the most of the insights derived from OPM. It is through this understanding that operators can have a clear understanding of performance, day-by-day and hour-by-hour. A mix of historical, real-time and predicted performance indicators can support decision making and speedier responses to unusual conditions.
Many food and beverage plants opt for custom-made modular solutions that are embedded with automation and operational technology. For instance, trusted automated elements like eddy current separators can separate non-ferrous materials from waste with a powerful magnetic field. Or, electromagnets can be used to recover tins and cans in combination with MESs.
Other modular approaches include fully automated material recovery facilities (MRFs). They are found to improve productivity and yield better quality recyclate while also allowing for greater flexibility to grow. Some operators regard the ideal as being an MRF that operates independently of human interaction. That said, the human element should not be completely disregarded in meeting waste management targets.
Some areas of the recycling process are still a long way from automation. For example, the pre-sorting and recovering of valuable materials, e.g. plastic, from municipal solid waste is still performed manually; although the process can involve cutting edge analysis equipment, like optical sorters, further down the line.
Europe’s largest anaerobic digestion plant
In the UK, AD technology is embraced as a valuable source of renewable energy, particularly for the purposes of converting waste food matter into bio methane and maximising the efficiency of generating gas from food waste.
AD is the breaking down of organic matter, in the absence of oxygen, with micro-organisms called methanogens. A digestion plant is very much like a human stomach and relies on a constant stream of food waste to keep going. This waste is broken down to produce energy-rich biogas — or methane plus carbon dioxide — and digestate. Otherwise the bacteria which breaks down the waste, dies.
The UK’s first AD plant is located at Cannock Chase, Staffordshire, and operated by the waste management firm Biffa. Biffa says that the 120,000 tonnes per year capacity facility, which cost £24 mn to build, is the largest of its kind in Europe. It mainly treats commercial and industrial food and organic waste from the nearby Sainsburys — specifically in the form of unsold food — and Bakkavor.
Biogas can then be used as a heating fuel for the plant itself or be converted into electricity by using a combined heat and power (CHP) unit.
Biogas is converted into biomethane or bio compressed natural gas (CNG) for use as vehicle fuel. It is also used to generate green energy that is then exported to the National Grid. Meanwhile, digestate can be used as a soil conditioner. Those are just some examples of how AD is fast emerging as a plausible way for food manufacturing plants to manage organic waste.
There would be no food waste, in an ideal world. Nevertheless, whether it’s through bespoke modular IoT solutions or inventive recycling technologies like AD, the continued marriage of processes and technologies in food and beverage plants can do their part to ensure that the $270bn goal to reduce food waste by 2050 is not a dream, but a reality.
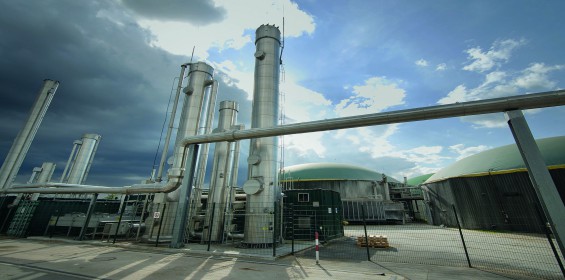