New for old?
Published: 04 December, 2019
Thomas Marks, Secretary at AEMT (Association of Electrical & Mechanical Trades), looks at what considerations should be made when it comes to repairing or replacing electric motors.
Decisions about repairs to any equipment usually revolve around two variables, time and cost; critical process machinery needs to be repaired quickly and the cost is offset by the loss of production. Speed is of the essence and in such cases, spare parts are usually held in stock, making replacement the obvious choice.
However, this opens up the opportunity to also have the failed component repaired without affecting the production schedule and providing a new spare component for future use. From this point, any process where repair time is slightly less critical, the option of rewinding the electric motor becomes a distinct advantage.
Assuming the design of the motor continues to meet the needs of the application, the severity of damage to the motor needs to be carefully assessed to determine the cost of repair. Damage to the stator core, the rotor or other mechanical parts will have a significant bearing on the final cost.
Most electric motors deliver a considerable period of service and during this time the application may have changed, and the technology used to build the motor will certainly have moved on. A breakdown offers the chance to assess the suitability of the motor design to the current application and make any changes that could improve reliability and efficiency.
One of the major advances is in insulation technology, which has enabled thinner layers to offer improved performance and efficiency, compared to materials being used two or three decades ago. Reduced insulation thickness allows for additional copper to be used in the windings, which can increase output.
This leads onto the next point, which is considering the amount of resources being used to return the application to normal operation. Replacing bearings, which resolves around 50% of motor failures, will double the life of the motor and use 99% of the original materials because the bearings are regarded as high-quality, green scrap.
By reusing, repairing, refurbishing and recycling existing materials and products, businesses can improve their environmental credentials. By encouraging a circular economy, businesses are taking responsibility for their decisions and actively reducing the amount of resources that they consume.
The breakdown of an electric motor never happens at a convenient time, but the situation can be turned into an opportunity to implement improvements at the same time as returning the application to normal operation. Since around 95% of the running costs associated with an electric motor are energy costs, the efficiency rating of the equipment should be carefully considered.
A new motor should offer an improved efficiency rating and therefore reduced annual costs, but a rewound motor can also offer several benefits. Having been rewound by hand, it is not subject to the errors of mass production and the windings will have been precision-made to give a perfect fit in the stator. Furthermore, research by the AEMT and EASA has shown that motors can be rewound several times while maintaining, or even improving, electrical efficiency.
Ultimately, motor reliability is the main goal as this will minimise downtime and the costs that are associated with it. By following good practice repair methods, those responsible for repairing electric motors can offer an invaluable service while at the same time reducing the amount of resources that are being used.
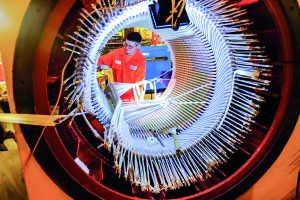