Rapid boiler feed pump repair ensures power generation reliability
Published: 24 April, 2023
At a time when national electrical grids are under extreme pressure, unexpected outages can prove to be a considerable challenge. When a power plant in Germany experienced the sudden failure of a boiler feed pump, output dropped by more than 40%, which affected both the local grid and company profits. Needing to resolve this situation urgently, Sulzer was called in to repair the asset and conduct an investigation to secure the reliability of the power station.
Thermal power plants rely on boiler feed pumps to supply large volumes of pressurised water to create the steam that drives the turbines. Keeping these vital assets in good order requires personnel to follow detailed operating procedures and planned maintenance programmes. Following on from the failure of the first pump in this particular power station, the worry of a second pump suffering from the same problem and ensuring overall reliability meant root cause analysis was as important as getting the facility back to full capacity.
Fast repairs
The power plant in question has two boiler feed pumps that have been in service for approximately 10 years without any issue. However, recently, the operator noticed a problem with the mechanical seals and called in Sulzer. The company responded immediately with specialist field service personnel on site the next day. Further investigation revealed that the pump was seized because of not following the correct start-up and maintenance procedures.
While the boiler feed pump was out of action, productivity from the plant was significantly reduced. Although the lost output from the power station was covered by other sites, the profit loss ran into multi-millions of Euros for every week the pump was out for repair. Considering the current demand for energy across Europe, time was most certainly of the essence.
“The first task was to explain to the plant management how the project would be delivered and the timeframe involved”, explains Claudia Calies, Service Centre Manager for Sulzer. “Clearly, the pump was required back in service in the shortest time possible and we have to manage this expectation and provide an accurate timeline for the work to be completed.”
Double shifts
From the first field service personnel on site to the last commissioning engineer leaving, Sulzer’s global network of technicians, engineers, designers, logistics specialists and project managers combined their OEM knowledge and service expertise to resolve this issue. Due to the highwater pressures involved, the pipe connections to the pump are welded, requiring a specialist to disconnect the 10-tonne pump. Once this was complete, the pump was removed and transported to Sulzer’s service centre in Jänschwalde to enable the necessary repairs to be completed.
The initial investigation found that the balance piston and sleeve were welded together, and this would require the shaft to be cut off and drilled out to separate the parts. The piston was replaced while a boring machine was used to bore out the sleeve to its original dimensions and complete the repair.
The Jänschwalde service centre staff worked two shifts per day to minimise the time required to get the pump back up and running.
Spare parts The plant operator had a stock of spare parts, including a new pump rotor, which had been ordered at the time of the pump’s installation. Considering the age of the rotor, it was sent to Sulzer to be inspected and to confirm its suitability for installation after 10 years in storage.
The repaired balance piston was then fitted together with the spare rotor, which had passed its inspection. All the additional spare parts required for the repair were also on-hand having been ordered for urgent delivery.
“Due to the important role of the pump, the power plant needed to have extensive documentation completed detailing all of the work carried out. This included independent checks and x-ray inspection of the new welds when the pump was reinstalled. The complex details involved in the repair of key pieces of equipment go far beyond the physical repair work, but Sulzer’s experience in maintaining all rotating equipment means that every aspect is covered in a turnkey project.”
The root cause
With the power plant running two of these pumps, the operator was very keen to identify the root cause of the initial problem to enable any additional preventative measures to be taken. During the inspection, there was evidence that a steam bubble was present in the area around the balance piston, indicating a lack of cooling and lubrication, which led to a massive rise in temperature.
Some information that was missing during the initial investigation was that the plant suffered an unexpected shutdown two or three days before the pump failure took place. Once the reason for the shut-down was resolved, the pump was restarted, however, during this process a procedural issue was determined as the root cause of the subsequent pump failure, confirming the operational reliability of the pump. As a result, having reinstated the pump and recommissioned it, Sulzer offered additional training for the plant personnel to try and prevent any reoccurrence in the future.
Stopping pump failure
In total, from the initial stoppage of the pump to recommissioning, the whole project was completed in nine and a half weeks. In contrast, the alternative would have been to order a new pump, but typically such a highly engineered asset would have considerably longer lead time.
Once the pump was reinstalled and operational, a review meeting was held to assess the performance of Sulzer’s team and the results achieved during the project. Although the operator had initially suspected that the pump might be at fault, it was concluded that the incorrect start-up procedure was responsible. The additional training and the checks that were carried out on the second pump have ensured that the scenario will not be repeated and that both pumps will continue to deliver reliable service.
Claudia concluded: “We regularly support the plant with annual shutdowns and communication between us is open and transparent, which is essential for a rewarding relationship.”
Following the successful completion of the project, the original rotor will be refurbished by Sulzer with a new balance piston being fitted along with refurbished impellers. This will enable the power plant to restock the spare part in case it should be needed in the future.
The project in numbers:
10-tonne pump
Up to 12 personnel involved
Time to complete repair: 9.5 weeks
Profit lost during downtime: Multi-million euro per week
https://www.linkedin.com/company/sulzer/
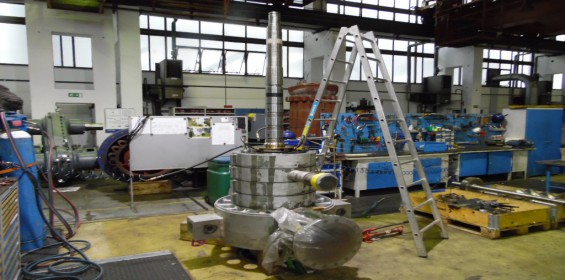
From the initial stoppage of the pump to recommissioning, the whole project was completed in nine and a half weeks