BCAS launches essential industry guide to compressed air installation
Published: 18 April, 2023
The British Compressed Air Society (BCAS) has launched a new compressed air installation best practice guide (BPG 101). As one of the only truly impartial guides in the UK, the guide covers ‘installation’ in terms of the collection of equipment and processes within the compressed air system. PWE reports.
Compressed air accounts for a considerable amount of electricity consumed by industry and compressed air systems are used extensively in virtually all industrial applications. The guide therefore provides essential information that can help readers reduce their energy consumption and ensure maximum uptime, while meeting legislative requirements to ensure health and safety is prioritised.
Providing step-by-step information for the correct specification, installation and maintenance of compressed air equipment as well as its end-of-life removal, the 272-page guide is essential reading for compressed air industry employees, plant engineers, maintenance technicians and end users.
The reliability of compressed air systems is a major consideration for operators, as any issues with supply can result in potential downtime. In addition, selecting the right equipment can be a complex task. It can affect everything from maintenance schedules and costs to ongoing air purity (quality), as well as the annual electrical energy cost of air production, which can be several times the cost of the original equipment.
The best practice guide is divided into a series of easy-to-read chapters to make specification as straightforward as possible. These cover compressed air system assessment, equipment selection and system design, including pipework. Detailed information is also provided around installation, commissioning, maintenance, system management, and finally, legislation and standards.
Vanda Jones, BCAS Executive Director added: “Our new best practice installation guide has been developed by experts in our industry to provide a complete and comprehensive suite of information for our sector and its compressed air users. Each chapter had its own dedicated working group made up of BCAS members and experts in the industry from both the manufacturer and distribution sectors, led by Tim Preece, BCAS’s Technical Officer to ensure the best information and product neutrality.
“The resulting guide is a fantastic, impartial resource for the sector.
“The components of a compressed air system must be selected and maintained with care. In many cases the system is a major consumer of energy and any decrease in efficiency will adversely affect the overall operating cost of the plant.
“Therefore, the correct choices when made early in the specification stage alongside the correct maintenance procedures, will have beneficial whole life cost and energy saving implications.
“We would like to extend our thanks to everyone who contributed to this guide, to make it the ideal companion for any users looking to improve the efficiency of their compressed air system.”
Companies can purchase the guide either as a PDF download or a hard-wearing, bound copy for £14.95 (plus VAT and postage) directly from the BCAS website https://www.bcs.org.uk/knowledge-base/bestpractice.aspx. For any other queries about the guide please contact the BCAS team at enquiries@bcas.org.uk.
10% Taskforce campaign – changing behaviours
In April last year, BCAS launched its 10% Taskforce initiative to encourage compressed air users to cut their energy consumption from compressed air by 10%.
In the first month alone, BCAS members demonstrated how they had helped customers save 5457 MWh in otherwise wasted energy – the equivalent of powering 1,800,810 homes for one hour – or 1631 homes continuously.
A compressed air system is just that; a system, and every element of it impacts on its energy consumption. Therefore, when exploring the potential savings that could be realised, it is important to take a full, system approach, – from generation to air treatment to distribution and finally, the point of use.
Change behaviours. Substantial efficiency improvements can be made by implementing new processes and encouraging staff to use compressed air more efficiently and safely.
Control better. BCAS members can advise on the best equipment and system for the application. This could include incorporating fixed and variable-speed drives or a combination of both as well as efficient downstream equipment.
Fix leaks. Reducing air leaks can have the biggest impact on overall system efficiency. Leak rates in industrial systems are typically between 20 and 40%, meaning the compressor must work harder, and therefore consume more energy, to compensate for the pressure loss.
Recover heat. As much as 95% of the energy consumed by a compressor is converted to heat and, unless captured, will be wasted to the atmosphere. Many manufacturers offer heat recovery systems, which can often be retrofitted. These recycle this excess heat; redirecting the hot oil to an oil-to-water heat exchanger.
Manage air downstream. Treating air to remove dirt, water and oil is necessary but can use a lot of energy. The process is likely to only need a proportion of the compressed air to be treated to a very high purity. In these cases, excellent savings are achievable by treating all the generated air to the minimum acceptable level and improving the purity (quality) to the desired level at the usage point.
Service and maintenance. Low cost, regular maintenance will help retain low leak rates and reliability of equipment. Operators should consider a policy that specifies that energy efficient options are purchased when replacing all equipment – whether it is a basic drain valve through to the actual compressor unit itself equipment.
For further information, please visit: taskforce10.bcas.org.uk
https://www.linkedin.com/company/british-compressed-air-society/
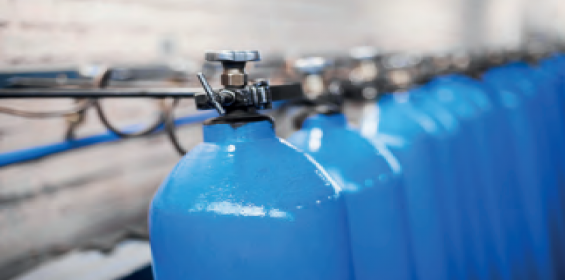