Free cooling – the cheapest and greenest way to provide cooling
Published: 07 February, 2023
By: Dave Palmer, general manager for the UK and Ireland at ICS Cool Energy
Improving industrial facilities’ systems performance has the attention of businesses and government organisations with good reason. Energy prices continue to rise. Organisations are focused on doing more with less, improving productivity, shrinking their environmental footprint and spending scarce capital budgets in ways that will provide the best return on investment.
The need to reduce economic and environmental impacts are making it important for manufacturers to implement strategies to reduce their energy consumption without hampering their critical function.
Process cooling technology continues to advance along with a sharper focus on total costs, energy efficiency and sustainability. Achieving the full potential of a process cooling system opens opportunities to save money and improve operational efficiency but requires a whole lifecycle approach that recognises opportunities to reduce total costs of a system, rather than focusing only on first costs.
What is free cooling?
The concept of free cooling is nothing new. In the old days, we cooled down our cars heated up by the sun by opening the windows, as the outside was colder than the inside. To some it may come as a surprise, but the same principle applies to free cooling in an industrial environment.
Any company or organisation using an externally sited chiller to cool their process can benefit from free cooling. Whenever the outside temperature is low enough to cool down the process fluid without the intervention of a chiller (mechanical cooling), we can implement a free cooling solution. This can be in the form of partial free cooling (where the chiller’s compressors are still doing some of the work to cool) to full free cooling (where the full load on the chiller is offset). In contrast, an externally sited chiller’s compressors with no free cooling capabilities will be working flat out to achieve the same.
Depending on the time of the year, as the ambient air temperature continues to fall, the amount of process heat taken out of the process fluid by the air increases, progressively reducing the load on the chiller. At 5 degrees Celsius below the process supply fluid temperature, all the process heat is removed by the ambient air in the free cooler – providing full free cooling. This makes free cooling the cheapest and greenest way to provide cooling.
When and how does free cooling work?
In the UK, Ireland and much of Western Europe, the relatively cool climate and ambient temperatures allow for partial or full free cooling for much of the year. This means that substantial energy savings can be achieved particularly between the months of October and April, in some cases reaching up to 80% electricity savings.
When the ambient air temperature drops just 1 degree Celsius below the process fluid return temperature, a 3-way valve diverts the returning process fluid through the free cooling coil in which the cooler ambient air removes process heat and cools the returning fluid (partial free cooling), it then flows through the chiller’s evaporator where the required set point temperatures are achieved – easing the demand on your chiller’s components and extending their operational life. Full free cooling is achieved in case when the ambient air temperature continues to fall, and the returning fluid from the free cooler meets the required process temperature.
Do you require a new chiller or can a free cooling solution be added to existing plant?
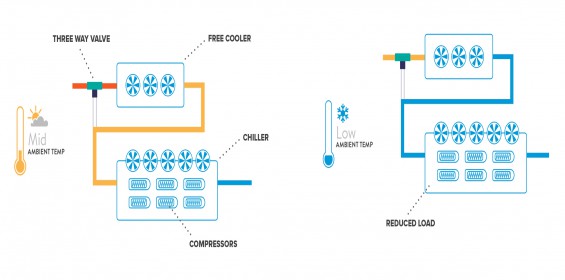
Free cooling works with either a chiller with a built-in free cooling coil or a free cooler working in series with a chiller. The latter is more efficient, due to the larger surface area provided by the air cooler.
A remote free cooler is designed to do nothing but provide free cooling and has its own purpose built control system and 3-way valve and bypass system and therefore is a simple and reliable way to give maximum savings and quick payback.
As the system is fully packaged, complete with integral controls, 3-way valve and actuator, and bypass pipe work, they can be easily installed on existing systems as well as new builds. Additionally, no communication between the free cooler and chiller is necessary, which in typical process cooling systems, allows to offload chillers for up to 90% of the year.
You can choose from solutions with multiple fixed fan speeds, inverter speed control and Electronically Commutated (EC) fans for varying noise applications. The units control panels are designed to offer ease of use with a ‘plug and play’ solution and 4G connectivity. They can be configured to meet your individual project requirements such as low noise, space restrictions and aesthetics and integrate with BMS.
The bottom line benefits of free cooling
In conclusion, free cooling is a concrete solution that will reduce mechanical energy consumption, lower the carbon footprint, reduce load on mechanical parts and therefore reduce maintenance cost and extend life of your cooling equipment. In case of a chiller, smaller load demands can also lessen the depreciation value of the unit over its lifetime. It is a solution that is easy to retrofit (space permitting) and can deliver a real quick payback for the new equipment.
Additionally, manufacturers looking to add free cooling into their systems, but trying to avoid capital investments, have the opportunity to benefit from programs like the ICS Cool Energy Flex. The equipment-as-a-service offer comprising a monthly package provides customers with running cost reductions versus the existing plant running costs. This type of a long-term solution is a fixed, hard-piped install to the customer’s process, offering energy savings, maintenance and annual cooling circuit fluid analysis and the option to upgrade as technologies improve. The flexibility of this business model can be a significant ingredient to the decision process and making a step into a more sustainable cooling.
https://www.icscoolenergy.com/
https://www.linkedin.com/company/ics-temperature-control/
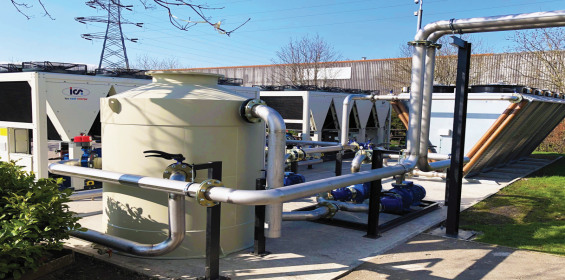