Automatic lubricators solution
Published: 16 October, 2020
Automatic lubricators and Arcanol grease ensure conveyor motor bearings run reliably at opencast mine. PWE reports.
By installing automatic lubricators for bearings on its conveyor drive motors and belt pulleys, an opencast mine in Hungary has seen a range of benefits, including prevention of unplanned downtime, longer bearing life and reduced repair work.
Energy provider Mátrai Erőmű ZRt. in Visonta operates one of the largest power plants in Hungary. Mátrai has a power generation capacity of around 950 megawatts and is supplied by the opencast mines in Visonta and Bükkábrány. In addition to lignite, the power plant also uses biomass, photovoltaics and natural gas. The plant employs around 2,000 people.
Challenge
At the opencast mine in Visonta, the drive motors that power the belt pulleys along 40 kilometres of conveyor belt are constantly moving. As a result, it must be ensured that lubrication – which is appropriate to requirements and capable of functioning under extremely harsh conditions – is used here. In the past, electrochemically driven lubricant cartridges were used for electric motors, however, a significant disadvantage of this solution is that the automatic single point lubrication systems do not always operate smoothly due to fluctuating outside temperatures.
Solution
Schaeffler engineers recommended the use of the CONCEPT2 two-point automatic lubrication system filled with Arcanol lubricant. This solution allows continuous and reliable lubrication of the bearings in the drive motors and belt pulleys, as well as in the paddle wheel in the excavator during operation.
These bearings include deep groove ball bearings, cylindrical roller bearings and spherical roller bearings. A total of 65 CONCEPT2 lubrication systems were installed for the electric motors. In addition, a total of 130 CONCEPT8 lubrication systems from Schaeffler are installed for the rope pulley bearings. The installation of the lubrication systems and the replacement of the lubricant cartridges was carried out by the local authorised Schaeffler sales partner, EuroBorsod Trade Kft.
The customer was particularly convinced in technical terms by the ease of operation and the robust design of the CONCEPT2 lubrication system. The primary benefits to the customer include prevention of unplanned downtime; longer bearing life; automatic lubrication irrespective of outside temperature; and a reduction in repairs. A further benefit is that the personnel assigned to manual lubrication can now be utilised for other important tasks at the plant. In 2020, Mátrai Erőmű ZRt. Plans to introduce further lubrication systems at the Visonta power plant for large fans and motors.
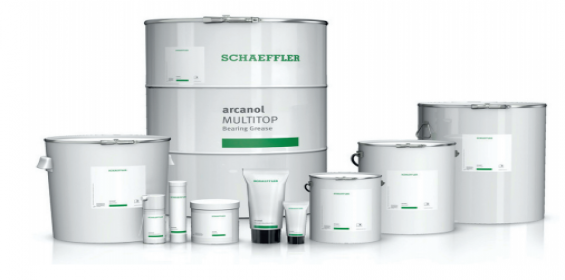