Factors influencing battery choice
Published: 09 October, 2018
Martin Walsh,senior application manager Motive and Reserve Power EMEA, EnerSys, looks at how to choose the best motive power source for electric warehouse and factory vehicles.
Many industrial applications depend on vehicles like forklifts, pallet trucks and personnel carriers to ensure quick, safe and efficient movement of stock and people. Increasingly, these vehicles are electrically powered and their potential depends heavily on the batteries and chargers they use for motive power. Hence, users have to consider key factors when they seek to purchase or upgrade vehicles’ batteries. Also, electric vehicle OEMs should look into these factors to ensure that their latest offering includes the best available battery solution that will meet customers’ needs. Key factors include consideration of lead-acid and lithium-ion (Li-ion) technologies and their variants, and Total Cost of Ownership (TCO).
Lead-acid battery technologies
A new type of lead-acid battery using technology known as Thin Plate Pure Lead (TPPL) offers OEMs and end users a practical and affordable alternative to both conventional lead-acid and Li-ion designs. TPPL resolves many of the lead-acid shortcomings, and allows users to achieve the productivity, economy and safety essential in today’s competitive environment.
The following are four key types of lead-acid batteries:
• Flooded lead-acid (Lead-Antimony)
• Valve regulated lead-acid (VRLA) Gel type (Lead-Calcium)
• VRLA – Absorbed Glass Mat (AGM) (Lead-Calcium)
• Thin plate pure lead (TPPL) (Pure Lead – VRLA – AGM)
Flooded lead-acid batteries provide good lifecycle, but their inherent design invokes many challenges. Charging is less than ideal because they require complete charging periods of typically 8-12 hours and overcharge of 10-20% to generate acid mixing and minimise stratification. Additionally, regular water top-ups are necessary. Fast charging, though possible, requires special chargers, accessorized for battery and charging algorithms.
Commercially-available VRLA batteries of both Gel and AGM type offer improvements. However, they have a limited charge acceptance capability, so require an extended charging time of around 8 – 10 hours. Current Gel products do not respond efficiently to fast charging high current recharge programmes.
The advantages of TPPL
TPPL is an enhancement over the other lead-acid batteries based on two core concepts, thin plates and pure lead:
• Thin plates: TPPL positive and negative electrodes are only 1 mm thin, compared to 9 mm in typical conventional lead-acid batteries. This allows many more electrodes to be fitted in the same space, increasing battery capacity and boosting power density. As a result, space requirement for the same capacity as AGM is reduced by about 30%.
• Pure lead: AGM VRLA batteries use a lead calcium alloy for their positive and negative plates. TPPL uses high purity lead, together with very high purity sulphuric acid. The chemical behaviour of the batteries is significantly more stable, which offers advantages relating to charging characteristics and lifetime. Also, the grain structure of the pure lead makes the plates far less susceptible to corrosion.
Like the earlier VRLA products, TPPL batteries are sealed types, with minimum gas and no need for water top-ups. This design imparts very low internal impedance to the batteries and allows both a very high rate of discharge, and quick, efficient acceptance of charge. Operating in Partial State of Charge (PSoC) mode therefore becomes possible. This is known as opportunity charging, because operators can use occasions such as shift changes or lunch breaks to charge at high current for short periods. Weekend full recharge with a cell equalisation will bring the battery pack to full State of Charge (SoC).
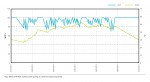
The batteries can be charged at rates within the range 0.4C5 to 0.7C5, or two to four times the standard AGM and Gel charging rates. Fast charge algorithms for cyclic applications are available for rapid and safe charging. PSoC operations can take place without adverse memory effects on the batteries.
Fig.2 shows data from a food manufacturing facility where a 6-day / 3-shift application was carried out using a 48V-625 Ah battery pack. Charging duration is representative of the time available during a typical shift operation. During this regime the battery operated in PSoC mode. On the sixth day, the battery was given an extended charge, with a constant current equalization to bring the pack to full-state-of-charge in order for it ready for operation in the following week.
TPPL also offers improved energy density. Figure 3 shows the relative volumetric energy densities at cell level.
Energy consumption is reduced, as the batteries require lower overcharging, at typically 8 – 10% compared with 10 – 20% for flooded types. Up to 30% energy savings can be achieved by using TPPL batteries with suitable chargers.
Another advantage is available to users who plan to hold spare battery stock for quick replacement of spent units. Unlike conventional batteries that must be recharged every six to twelve weeks during storage, TPPL types can be stored for up to two years at 20°C when starting from a fully-charged condition. This reduces resources spent in monitoring the open circuit voltage of batteries in inventory and boost charging those that need it. Figure 4 quantifies battery performance during storage.
TPPL’S TCO reduction
TCO savings arise from both opportunities to streamline daily operations, and the improved battery technology. As motive power technologies support fast charging and PSoC operations, vehicles can remain actively productive for far longer without needing to stop for an extended charge period. As a result, multi-shift operation is possible, without requiring the space, capital costs and labour associated with stocking, maintaining and exchanging spare batteries. Furthermore, the costs and space needed for dedicated charging rooms, and truck routes to them, are eliminated as the TPPL batteries can be charged in situ.
Maintenance costs are further reduced, as time previously spent on frequent water topping up is saved. Energy costs also come down, as TPPL batteries require less overcharging than flooded cells. Once in use, the batteries provide a longer cycle lifetime than standard AGM and Gel types. Meanwhile, higher performance and better energy density allow for the specification of smaller, lower-cost batteries, while saving space within vehicles.
Li-ion: waiting to fulfil its potential?
Li-ion batteries’ sensitivity to certain operating conditions and external factors mean they require electronic battery management systems, which contain the algorithms to operate the cells in a safe, controlled and optimized way, including shut down capability. Li-ion suppliers have claimed virtually zero maintenance, high power density and flexible charging as advantages over traditional lead-acid solutions – but these advantages are also found using TPPL. That said, Li-ion products do have an extremely high lifecycle, so they often outlast industrial trucks and can sometimes be re-used.
While lead-acid batteries are easily and virtually completely recyclable, disposing of Li-ion batteries presents a greater challenge. Nevertheless, major progress has occurred at a pilot plant level to enhance the recyclability of Li-ion and it is anticipated, in the next few years, that a more consistent and cost-effective method to recover important raw materials from the primary compounds may be established.
Conclusion
The advantages from TPPL are significant enough to transform materials handling in warehouses and factory areas. Motive power users and OEMs now have interesting choices. Lead-acid’s many decades’ proven performance remains competitive through recent advances like TPPL, while Li-ion is an alternative that could become increasingly attractive as future developments become commercially available.
For further information please visit: www.enersys.com
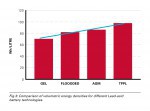